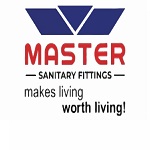
Master Poly Plastic Industries Limited
It is the manufacturer and wholesaler of sanitary products and Related plastic accessories, including bathroom accessories, PPRC, and UPVC pipes.
Before implementing 9T9ERP, Master Poly Plastic Industries Limited typically faces several challenges:
- Inventory Management: Difficulty in managing raw materials, components, and finished products efficiently due to disparate systems or manual processes.
- Production Planning: Lack of real-time visibility into production schedules, leading to inefficiencies in resource utilization and meeting delivery timelines.
- Quality Control: Inconsistent quality standards across production batches, impacting customer satisfaction and operational costs.
- Supply Chain Coordination: Challenges in coordinating with suppliers for timely delivery of materials and components, affecting production continuity.
- Sales and Order Management: Manual processes for order processing, invoicing, and tracking sales orders, resulting in delays and errors.
- Financial Management: Limited visibility into financial performance, cash flow management, and profitability analysis due to fragmented systems.
- Regulatory Compliance: Difficulty in complying with industry regulations and standards without integrated systems for tracking and documentation.
- Data Security: Concerns over data security and confidentiality, especially with sensitive information related to product designs and customer details.
- Customer Service: Challenges in providing timely and accurate information to customers regarding order status, deliveries, and product inquiries.
- Employee Productivity: Lack of integrated tools and systems for project management, collaboration, and performance tracking, impacting overall productivity and morale.
Addressing these challenges through the implementation of 9T9ERP can streamline operations, enhance efficiency, improve decision-making capabilities, and ultimately drive growth and profitability for the sanitary ware manufacturing company.
Solutions Provided by 9T9ERP Against Challenges Faced by Sanitary Ware Manufacturing Companies
- Inventory Management: Centralized inventory control with real-time visibility and automated replenishment triggers to optimize stock levels and reduce wastage.
- Production Planning: Advanced production scheduling tools that synchronize demand forecasts with manufacturing capabilities, improving resource allocation and delivery timelines.
- Quality Control: Integrated quality management modules to standardize processes, track defects, and ensure consistent product quality across batches.
- Supply Chain Coordination: Streamlined supplier management with automated purchase order generation, supplier performance tracking, and real-time communication to prevent delays.
- Sales and Order Management: Efficient order processing, invoicing, and sales tracking through integrated CRM and order management modules, reducing errors and speeding up fulfillment.
- Financial Management: Comprehensive financial reporting and analysis tools for better cash flow management, profitability tracking, and compliance with accounting standards.
- Regulatory Compliance: Built-in compliance features that help adhere to industry regulations through automated documentation, audit trails, and regulatory reporting.
- Data Security: Robust data encryption, role-based access controls, and secure cloud infrastructure to safeguard sensitive information and ensure regulatory compliance.
- Customer Service: Enhanced customer relationship management capabilities with integrated customer support tools for faster response times, accurate order status updates, and personalized service.
- Employee Productivity: Unified platform for project management, collaboration, and performance tracking, fostering teamwork, efficiency, and employee satisfaction.
Benefits of 9T9ERP After Implementation
- Operational Efficiency: Streamlined processes and automation lead to reduced lead times, lower operational costs, and improved resource utilization.
- Enhanced Decision-Making: Real-time analytics and reporting provide actionable insights, enabling informed decisions and proactive management.
- Improved Quality: Consistent quality control measures ensure product reliability, leading to higher customer satisfaction and retention.
- Scalability: Ability to scale operations and handle growth seamlessly, adapting to market demands and expanding product lines effectively.
- Compliance Adherence: Simplified regulatory compliance processes ensure adherence to industry standards, reducing risks and enhancing credibility.
- Customer Satisfaction: Faster response times, accurate order processing, and personalized service contribute to improved customer relationships and loyalty.
- Cost Savings: Optimized inventory levels, efficient resource allocation, and reduced operational inefficiencies contribute to overall cost savings and improved profitability.
Implementing 9T9ERP transforms challenges into opportunities, enabling sanitary ware manufacturing companies to achieve operational excellence, competitive advantage, and sustainable growth in the industry.